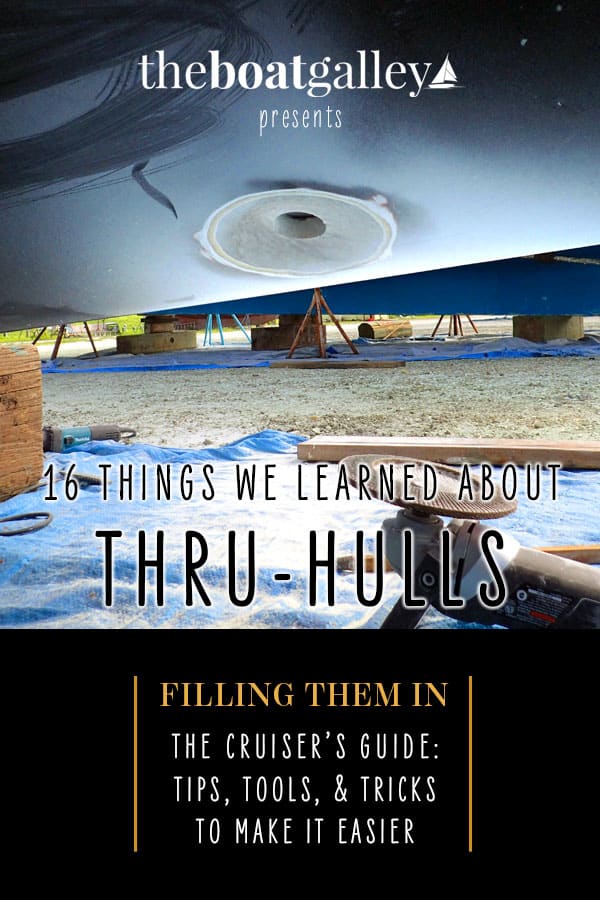
Want a few tips on filling in a thru-hull?
This isn’t going to be a “how-to” on the project. You can get great information both in Don Casey’s Complete Illustrated Sailboat Maintenance Manual and on the West Systems website. Nope, this is the stuff about filling in a thru-hull that either someone did tell us and was extremely helpful or that we wish someone had told us. (Links are to Amazon to show the products discussed in case they’re new to you – several were new to us – but you can get most of the items at hardware and home improvement stores.)
- Protective gear. Get and wear protective gear from the start: sanding/particle masks, a bunny suit (Tyvek is best but one that’s breathable may be more tolerable in summer heat), goggles, and gloves (latex are fine if you’re not allergic to it). The materials for filling in a thru-hull are both itchy and hazardous. Dave added a paint spray hood when he was doing the worst of the fiberglass grinding to keep the dust from getting around his neck. Get plenty of masks and gloves – we had 10 masks (about right) and 15 pairs of gloves (could have used more)
- Second person. You can fill in a thru-hull single-handedly and many portions (grinding . . .) are really one-person jobs. But when you start working with epoxy and fiberglass, a second set of hands is really helpful. The second person will be working with fiberglass and colloidal silica, so get protective gear for them too (if nothing else, make sure anyone who is near the colloidal silica wears a particle mask – it’s bad in your lungs!).
- Wood plug. If your thru-hull is like ours and has a thick wood backing plate, a good way to fill that hole (not the hole in the hull itself but the inch or so extra through the wood) is to use a hole saw of the appropriate diameter and cut a wood plug that you can epoxy into place. Don’t let it intrude into the fiberglass hole of the hull and use thickened epoxy to secure it. If needed, put a screw into the drill hole left by the hole saw to hold the plug, then after the epoxy has cured, remove the screw and fill that hole with epoxy. Then apply a few layers of fiberglass cloth and epoxy on the inside over the whole backing plate.
- Showers. You’re going to be working with fiberglass every step of the way, from grinding it to cutting and applying layers of it to sanding it again. The stuff is nasty, itchy and painful on your skin. As soon as you finish for the day, take a cool (not hot!) shower and change into fresh clothes. Don’t wait! (Related and possibly TMI: be careful going to the bathroom that you don’t get fiberglass shards on your genitals. It hurts. Badly. For days.) Do not even think of filling in a thru-hull in a boatyard without a reasonable shower.
- Time. This project – filling two thru-hulls – took about 10 days but part of that was that we did it in the middle of summer when it was brutally hot and we just couldn’t work out in the sun more than about 4 hours a day. But some of that time was that we couldn’t apply too many layers of fiberglass and epoxy in a day so that it would cure properly (we did 13 layers a day). Grinding and sanding is hard work, too. And cleaning up each day – both yourself and the work area – takes time. It’s not going to go as fast as you might expect. And you want to do it right – this is a hole below the waterline, after all.
- How many layers in a day? The books say not to do too many layers at a time due to the heat that builds up in the curing epoxy. There’s also the weight of the wet fiberglass/epoxy and the fact that you’re probably working on a vertical to overhead surface — you don’t want gravity to start making the fiberglass slip (note: Don Casey mentions holding the fiberglass cloth with masking tape when working on a vertical surface; this created a huge mess for us and we found we were better off with just epoxy to hold the cloth). Theoretically, you can do some layers, let it start to cure, do some more, let it start going off, etc. and do the whole layup in a single day without having to do any sanding or between-coats prep. We were exhausted long before then and so had to prep the cured layers from the previous day each morning by sanding and washing with acetone. Typically we did 6 or 7 layers in one hole, then the same in the other hole, took a break, then did 6 or 7 more layers in each hole before calling it a day.
On to tools that we found helpful, tips and amounts of things we used. This list is not complete – you’ll see other things mentioned in the “how to” articles. This is just the extra stuff we wished we’d known . . .
- Flap disk. The instructions say to grind the fiberglass out to a diameter 12 times the depth you are going to fill. A friend at the boatyard here told us about a great tool to do this with – a “flap disk” (sometimes called a flap wheel) on a buffer/sander. Dave first used a 4” diameter 36 grit one to get things started, then switched to an 8” diameter to finish it. NOTE: Neither Dave nor I had ever seen or heard of these (and my dad owned a hardware store!) so here’s a photo — it was a HUGE help. Ace Hardware had them in stock and so do places like Home Depot and Lowe’s.
- Sander. Because we had to do the fiberglassing over three days, plus a fourth for adding a fill coat at the end, Dave had to sand the previous day’s top layer before starting the next one. Lots of 80 grit sandpaper was used (don’t use the flap disk here, it’s too aggressive) – maybe 30 discs?
- Acetone. Both to prep the surface each day and to clean things up. Two quarts. And lots of rags and blue paper towels. Plan to throw the rags out; don’t try to wash the epoxy out of them.
- Brushes. We first tried using throwaway foam brushes. Don’t bother – they’re horrible with epoxy. Use cheap bristle brushes (we used 1” and 1-1/2”) and buy enough that you can use at least two new ones every day. We also had a squeegee and used it “some” but the brushes were the work horse of the project.
- Epoxy pots. If you mix a fresh batch of epoxy in a pot with some left in it from the previous batch that’s going off, the new batch will also go off almost immediately. (Ask us how we know.) Using a fresh pot stops this. But you can re-use the pots the next day – just pop the cured epoxy out. The pint Mix ‘n Measure pots worked well for us and held up – the brand isn’t important but some are not chemically resistant. Don’t use red solo cups. We used three.
- Epoxy pumps. Epoxy pumps are worth the money to get the mix right every time. Just leave them in the cans until the project is done; don’t bother to clean them every day as you’ll waste a lot of epoxy, acetone and time. We found that “two pumps” each of epoxy and hardener was about the right amount to work with (your preference may be different but it’s a starting point). NOTE: Different brands of epoxy use different ratios of resin to hardener. Be sure to get the same brand pumps as epoxy.
- Epoxy amount. Every boat will be different with the size of the holes and the hull thickness, but on a relatively thin-skinned catamaran we used over a quart of resin to fill two thru-hulls (and the corresponding amount of hardener).
- Fiberglass. Wow! Did we ever underestimate how many layers we’d need – we’d thought at most maybe a dozen, and ended up using 39 per thru-hull! We could only get 6 oz. cloth (not the 10 oz. that Casey recommends) but it was amazing how it thinned out the minute it was wetted with epoxy. We used almost 3 square yards of fiberglass fabric on the two thru-hulls. Others filling thru-hulls in our yard have said the same thing — they expected to use 6 to 12 layers from what they read, and ended up with anywhere from 30 to 60+.
- Fiberglass circles. Yes, I cut 78 circles from fiberglass cloth.
- Don’t cut the fiberglass in your lap unless you have several layers of protective fabric between the fiberglass and your legs – a large piece of cardboard is good.
- The circles will go from the size of the thru-hull to the full circle you ground out. Don’t worry too much about being exact – the fiberglass cloth is very loose weave and pulls and distorts as you put it on and soak it with epoxy.
- Fold two or three layers of fabric together in quarters and then cut a quarter circle – much faster and easier than trying to cut a full circle.
- Don’t be surprised if you end up putting smaller on top of larger, etc., as you see how the layup is going. A couple of times we discovered we needed to go back smaller to keep things level.
- Straight edge. A straight edge that’s long enough to span the entire ground-out area will help as you lay the fiberglass, both to keep it level and to let you know how full the hole is (or isn’t). An old 18″ metal ruler worked well for us. It also helps when you’re doing the final fairing with epoxy/silica and then sanding.
Finally, check with the tech support people for whatever bottom paint you use to determine whether you need to use any sort of primer before applying bottom paint to the “new” hull area.
Read Next
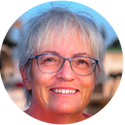
Carolyn Shearlock has lived aboard full-time for 17 years, splitting her time between a Tayana 37 monohull and a Gemini 105 catamaran. She’s cruised over 14,000 miles, from Pacific Mexico and Central America to Florida and the Bahamas, gaining firsthand experience with the joys and challenges of life on the water.
Through The Boat Galley, Carolyn has helped thousands of people explore, prepare for, and enjoy life afloat. She shares her expertise as an instructor at Cruisers University, in leading boating publications, and through her bestselling book, The Boat Galley Cookbook. She is passionate about helping others embark on their liveaboard journey—making life on the water simpler, safer, and more enjoyable.
Your VHF can do so much! Learn how to use ALL its features for just $39:
John Huft says
I like the thick nitrile gloves from Harbor Freight. Also dust a little baby powder in the gloves and on your hands before you put your gloves on. The baby powder absorbs the sweat from your hands and the gloves are easy on and off. You can also use baby powder as a thixogen in a pinch.
Joie de Vivre says
I use Red Solo Cups all the time for epoxy and have not had a problem. The wet epoxy is not in the cup long enough for it to melt the cup. These cups cannot handle the heat of kicking off though.
Bert Sailor says
Y en a pas de p’tites jobs!
The Boat Galley says
C’est vrai!
Frances Liz Fernandez says
Very informative. Not sure we are skilled enough to attempt to take on this project but good to have these tips.
The Boat Galley says
We’d done a little fiberglass work and some epoxy but we weren’t really experienced. Take it slow and easy and you can do it!
Andrew Hogg says
I know that getting a boat yard to fix this for you would be very expensive. It looks to me like you now know WHY it’s very expensive. Fibreglass is, as you made sure to highlight, nasty stuff. For all of it’s great properties, it’s dangerous and uncomfortable if not handled correctly. I think you were brave to tackle this job yourself. Well done! And thanks for sharing the tips. After this article, I hope I never need them!
Carolyn Shearlock says
Yes, and we’re in a do-it-yourself boatyard so no one to hire, really (there is a shop next door but the guy is backed up with work for quite a while).
Stephanie says
Carolyn, You and your husband do an amazing job at whatever you set your mind to! Love these explanations- SO helpful for anyone attempting this!
Carolyn Shearlock says
Thanks! I try to pass on all the info I wish I’d found before we started. 🙂
Melissa White says
Great information! Galapagos has way too many thruhulls. I lost count. One of our goals in taking care of her is to reduce the number of these holes. I’m bookmarking this one!
Brian Hollinger says
Thank you for this. I don’t like where any of my thru-hulls are and will eventually be moving, or filling, *all* of them…
The Boat Galley says
Ugggh . . . big job!
Desiree Golen says
We learned that coating our arms, legs and neck with baby powder before every project was a great way to keep those inevitable shards from getting on our skin!
Kimberly Boneham says
This is very timely as we’ll be starting this exact project next weekend. Thank you!
Helen Murdoch says
Next time try white vinegar instead of acetone, especially for cleaning your selves. The effectiveness of this versatile product is amazing. We are amatuer boat builders and intitially only used acetone. Now we only use acetone when a tool is required to be cleaned and immediately used as the acetone drys quickly. Friends that have helped are amazed at the effectiveness of vinegar.
Carolyn Shearlock says
Thanks — we’ll try it.
Daniel says
Great info.
I have two seacocks to remove and patch up that used to go to the old head. (removed for an Airhead)
Carolyn Shearlock says
You’ll do okay . . . it’s not horrid, just a lot of stuff we wish we’d known before we started.
mike hogan says
Any reason you choose to use epoxy instead of fiberglass resin? resin cures much faster(typically) than epoxy and i have always been told that it is better to go back to use the same type material when possible.
Carolyn Shearlock says
Epoxy has the best adhesion to the existing surface. Our boat was originally built with vinylester. In general, “fiberglass resin” (Bondo) is not used for boat repairs. Click here for a good article by Don Casey, author of “This Old Boat” on the differences.
Becky says
Imagine our horror at discovering during a haulout to prep and bottom paint our Ericson 32…. I was wet sanding the bottom, when I discovered a circular ring in the thin bottom paint, that was oozing water. This was below the head, below the waterline. My husband and I investigated, and concluded what happened in the Calif. construction yard: some worker drilled for a thru-hull, then found out it was in the wrong place. He merely replaced the plug with common bathtub calk, and hid it with the first coat of bottom paint. The only thing holding that plug in after the calk failed was the bottom paint! Imagine if it was pushed inside at sea!!!! We almost fainted, and did a proper fix. Horrors.
Ucluelet Charters says
Great article looking to fill in a couple through hulls on one of our boats. Live bait wells we don’t use out this way better used for storage.
Stuart G Cole says
There is no reason to use epoxy in this case, or in most boat repairs, yet amateurs seem to gravitate to it because of marketing, mostly. Its equivalent to using titanium to repair your car body. Polyester resin is far easier to use, and its what the boat is made of (okay vinylester, so get vinylester resin if you want – the stress on this area is negligible). One can control the thickness (run, sag), and the cure time. And if you use an air inhibited laminating resin it eliminates sanding between coats, a huge time saver. Also get some thick biaxial mat/cloth. Granted I have long experience in fiberglassing boats, but this project would take me about 3 – 4 hours max including final sanding and coating, if I really cared since it will be covered by bottom paint anyway. I do like your tip to use a flap disk, that is great.
Carolyn Shearlock says
We went with epoxy on the advice of Don Casey as the resin is also gluing the patch to the nearby surface. Here’s Casey’s analysis of which to use when:
http://www.boatus.com/boattech/casey/polyster-epoxy.asp
Jeanie B. says
Great post, Carolyn! I worked in a boat building and repair yard and for this repair we also would use polyester resin. We use epoxy/fiberglass layers for gashes in hulls, etc. But good on you, those areas are now stronger than original. Ditto on the flap disk.
Kim Gibson says
Wondering if there’s a way to save this post!
The Boat Galley says
Bookmark it, or just know that it’s on The Boat Galley and you can use the search feature on the site to find it again. Also, supposedly if you SHARE it here on Facebook it will be saved on your timeline.
Lindy Duncan says
You can “save a post” on fb. In the right hand corner above the picture, there is a little arrow. Click on it and a dropdown menu appears. You should have the option to save the post there.
The Boat Galley says
Thanks!
Montana Inkfish says
Great overview. Thanks!
Jeff Ferguson says
I decommissioned one simply by securing plugging the bronze thru hull. Does the job and the thru hull might come in handy for something else down the road.
Matthew Bastian says
Epoxy pumps are not as accurate as you might think! They do a good enough job that your epoxy will cure and you won’t notice the difference but if you really want a 100% ratio dispense by wight or a graduated measuring device.
If you want to be shocked, try pumping into container sitting on weigh scale and note the variations from pump to pump. The first pump of a session will always be the worst. Pour it all back when done the experiment.
BTW. Really enjoy your site and find it very helpful. I consult it regularly.
Ritchard Findlay says
I have done a number of thru hull jobs like this. One trick I use is to go grab a piece of the heavy plastic sheet that we use to wrap boats in winter in the north – you southerners can find some other heavy piece of plastic sheet. When you are ready to place your fibreglass patches, wet out the hull a couple of inches larger than the hole. Place your patches per normal, then cover them with a chunk of the heavy plastic that same 2 inches larger than the repair. The plastic sticks to the epoxy tenaciously, holding the patch in place, but it will peel off fine in the morning. The excess epoxy that held the plastic sands away easily.
The Boat Galley says
Great idea!
Dave Chittleborough says
Why not do it properly and use peel ply. Then you don t need to sand before painting 😜
Ritchard Findlay says
Dave Chittleborough If I had peel ply, I’d use it. I have shrink wrap.
Pierre Mitham says
Dave Chittleborough Peel ply doesn’t prevent the need for smoothing completely but it does greatly reduce it. the West guide on this is great!!
https://www.youtube.com/watch?v=6N7YMr6E564
Ritchard Findlay says
But come to think of it, shrink wrap would work better for this purpose than peel ply. Much much heavier gauge.
Pierre Mitham says
Ritchard Findlay if you can’t find peel ply, go to fabricland and by a couple of yards of polyester dress lining. Works exactly the same and only costs about $5 a yard!
Pierre Mitham says
Seems like a long time (10 days) to fill in a thruhull. With slow set hardener I was able to do 7 in 2 days. smend the morning with the grinder and flap wheel to create the tapers in the patch, then the afternoon to cut the patches (I used biaxial 1708 for 15 layers on my hull) then the next day, apply the internal partches, then grind and smooth the outside to a finish for barrier coat.
The Boat Galley says
If we ever do it again, we’ll use heavier fiberglass fabric if we can get it. Nowhere nearby had it, so we used thinner fabric. We would have been a lot better off to order thicker and wait for it.
Pierre Mitham says
1708 is much easier to work with, stronger and neater. 15 layers is almost 3/4 inch thick!
The Boat Galley says
I keep learning . . . thanks for all the better ways to do it! More stuff that’s not in the books and websites I was referring to!
James Delane says
Acetone is not very healthy. Also, when you use acetone to clean any epoxy that gets on your skin, it leaves a sticky residue. If you accidentally get epoxy on your skin, use vinegar to get it off. It is easier on your body and leaves no residue. Clean the epoxy off with vinegar and clean the vinegar off with a nice smelling soap and water.
Tami says
THE bible:
https://www.westsystem.com/wp-content/uploads/Fiberglass-Manual-2015.pdf
Paul Mac Menamin says
One thing I found very helpful was to get a “Easy Cutter” electric scissors. Makes cutting 1708 a breeze. Available from Jamestown Distributors
Scott says
Be VERY careful with vinegar inside a boat. Vinegar can and will soften or dissolve cured resin as well as uncured. Clean up any spills immediatly, rinse and clean up the water.